
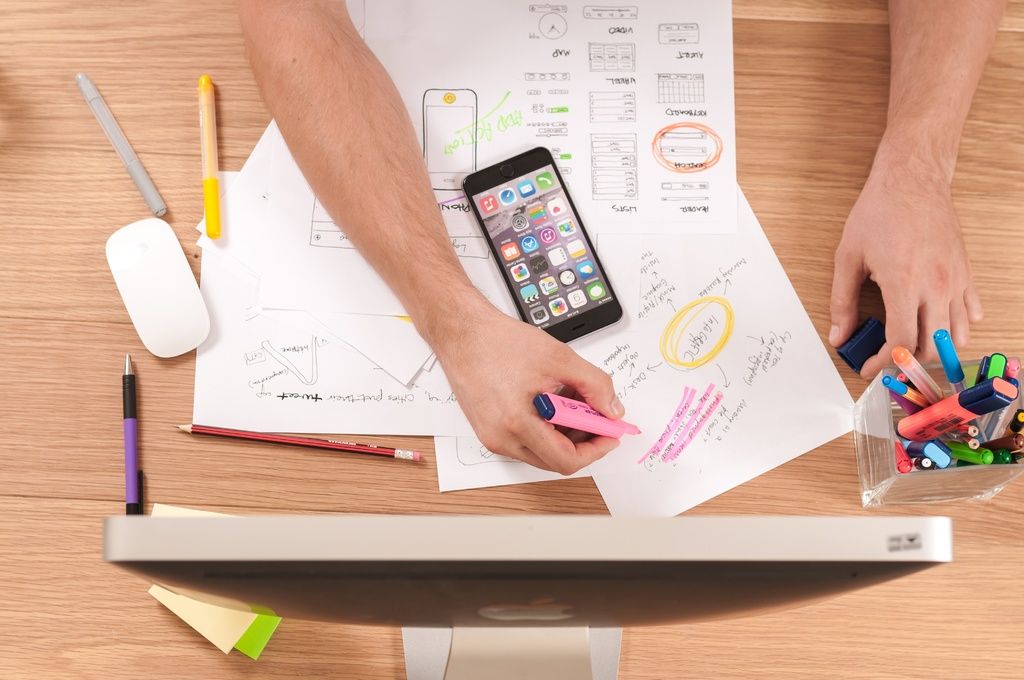
#Webdesign arnhem full
(Don’t stuff it too full or the wash won’t get properly clean.) Put the laundry in the washing machine.Buy a washing coin using the exact change: it’s €5.50 per coin and the large machine needs 2 coins.The final solution of the joints was computed using IDEA StatiCa Connection. Connections for assembly only with bolts (no welding on site).Outside of construction is not allowed the accumulation of dirt, leaves, etc.No steel connected unwelded allowed, not even internally (both sides fillet welds or butt weld).Thermal galvanized construction needs ‘sinkholes’ ≥ 30% of the cross-section.The connection needs to withstand normal force N c,Rd = 2818 kN.The segmentation bottom ring has a dimension Ø 323,9 x 8 S355J2H, conditions demanded by the client were as follows: This ring is supported by pendulum columns and diagonal bracing has been applied between the columns. Special constructive cleverness / detailsĪt the edge of the dome, the net structure comes together in a ring. All columns are braced during the assembly and during the assembly of the dome construction, the draw beam is every two columns.

Here and there a wind bracing has been applied between the columns. The columns have different lengths due to the change of the ground level. The bottom ring is supported on its own by steel columns, HEA 240 profiles, which, as already indicated, are spaced between 4.50 and 5.00 m. For these coupling pieces, tight dimensions and accuracy were also required, because the position of these connections was again different for each main tube due to the curvature of the dome. Short pieces of the tube are welded to this with a bottle plate on the head. The main tubes of the dome are flanged to the bottom ring. This beam is also made up of prefabricated parts, which are connected with welded flanges of 40 mm thick, for extra safety. It is composed of the same tubes as the main girders: tubes with a diameter of 323 mm and a wall thickness of 8 mm. The bottom ring absorbs all forces from the dome. After the dome was closed, the auxiliary structure was removed. This was necessary because the dome only gains its strength when the dome construction is actually closed. During the assembly of the main pipes and the struts, the whole was temporarily supported by three auxiliary structures. This required precise dimensions and work, because each fork joint is at a different angle due to the double curvature of the dome. The plates of these connections are prefabricated to the main and strut pipes. The struts are connected to the main pipes with fork joints. This is because the entire construction is exposed to outside conditions because the actual roof sealing hangs underneath.īetween the main pipes, there are diagonal strut connections, consisting of pipes with a diameter of 193 mm and a wall thickness of 8 mm. An important detail is that the flanges in the heart have so-called dezincification holes to prevent deterioration of the hot-dip galvanized steel. The parts are coupled with flange connections with every ten bolts. The largest span consists of five prefabricated pieces with an average length of 13 meters the smaller spans consist of fewer pieces. The tubes do not run parallel to each other due to the double curvature of the dome, but generally, they are about 4 meters apart. The dome is spanned in one direction by steel pipes with a diameter of 323 mm and a wall thickness of 8 mm. Steel appears to be much better suited for the required high tensile forces in the bottom ring. A timber construction would greatly reduce the incidence of light due to its large profile dimensions, creating a lot of shadows. Steel was chosen because this eco-display requires a lot of daylight. The dome structure is designed in steel, which is remarkable in itself, as many of these structures are designed in wood. At the lower parts of the dome, there is sufficient remaining height to use the space functionally and the surface of the vertical facade is kept to a minimum. The construction is highest in the middle, which makes the experience of the eco display optimal and makes tree growth possible. The chosen arc-shaped roof construction fits in well with the above-mentioned requirements. In addition, the construction had to be realized on the outside, just like with Burgers 'Bush and Burgers' Desert. For the mangrove hall, the biggest consideration during the design was a careful choice between a surface as possible for the presentation of the eco-display within an optimal building shape and, on the other hand, a volume as large as possible, whereby the construction costs are controlled by the smallest possible facade/roof surface.

Description of steel construction and/or use of steelĭesigning is an integral process in which choices are weighed.
